The aim of the BioElast 01 (A03) project was to develop adaptive, elastically deformable fiber-reinforced composites with adjustable stiffness properties without increasing the material input and the weight of the elements for use as large-scale façade shading elements. The possible deformation and stiffening of planar components made of fiber-reinforced composites was investigated by integrating rod-shaped pneumatic actuators.
In contrast to technical motion mechanisms, movements in plants are not achieved by rigid-body mechanisms, i.e. mechanisms in which rigid links are connected to each other by kinematic connections, but by compliant mechanisms. They achieve their functionality through controlled deformation of elastically deformable elements. In this project, stemmed plant leaves were used as a biological role model. Due to the gradual transitions, the external shape and the vein network in the leaf itself, which is responsible for leaf unfolding and shape stability, they proved to be an ideal role model. The connection between the petiole and the leaf blade is furthermore a damage-resistant connection.
Within the project, the plant actuation principle as well as the integration of the actuator were successfully transferred into a technical façade component. It was also shown that the pneumatic actuation of fiber-reinforced composites out of one plane results in a curvature of the same, which leads to a stiffening of the overall structure. For the application as a façade shading component, this means an increased resistance to wind and snow loads. The project's demonstrator FlectoCurve shows various forms of such integration of pneumatic actuators and is described in detail separately here.
Project Duration
Juli 2019 – Juni 2023
Project Team
ITKE Institute of Building Structures and Structural Design
University of Stuttgart
Prof. Dr.-Ing. Jan Knippers, Mona Mühlich, Axel Körner
ITFT Institute for Textile and Fiber Technologies
University of Stuttgart
Prof. Dr.-Ing. Götz T. Gresser, Dr.-Ing. Larissa Born
PBG Plant Biomechanics Group, Botanical Garden
University of Freiburg
Prof. Dr. Olga Speck, Max Langer
Publications within the scope of the project
Langer M, Kelbel MC, Speck T, Müller C, Speck O (2021) Twist-to-Bend Ratios and Safety Factors of Petioles Having Various Geometries, Sizes and Shapes. Front Plant Sci 12:765605. https://doi.org/doi:10.3389/fpls.2021.765605
Langer M, Speck T, Speck O (2021) Petiole-Lamina Transition Zone: A Functionally Crucial but Often Overlooked Leaf Trait. Plants (Basel) 10(4). https://doi.org/10.3390/plants10040774
Langer M, Hegge E, Speck T, Speck O (2022) Acclimation to wind loads and/or contact stimuli? A biomechanical study of peltate leaves of Pilea peperomioides. J Exp Bot 73(4):1236–1252. https://doi.org/10.1093/jxb/erab541
Mühlich M, González EA, Born L, Körner A, Schwill L, Gresser GT, Knippers J (2021) Deformation Behavior of Elastomer-Glass Fiber-Reinforced Plastics in Dependence of Pneumatic Actuation. Biomimetics (Basel) 6(3). https://doi.org/10.3390/biomimetics6030043
Speck O, Langer M, Mylo MD (2022) Plant-inspired damage control – An inspiration for sustainable solutions in the Anthropocene. The Anthropocene Review 9(2):220–236. https://doi.org/10.1177/20530196211018489
Wolff-Vorbeck S, Speck O, Langer M, Speck T, Dondl PW (2022) Charting the twist-to-bend ratio of plant axes. J R Soc Interface 19(191):20220131. https://doi.org/10.1098/rsif.2022.0131
Funding
This research was funded by the Ministry of Science, Research and Arts (MWK) Baden-Württemberg within the program ZO IV: Chapter 1222 TG 90: Focus field "Establishment and strengthening of research infrastructure in the field of micro- and nanotechnology and new materials" within the joint project "Bio-inspired elastic material systems and composite components for sustainable construction in the 21st century"/BioElast 01 (A03).
Contact
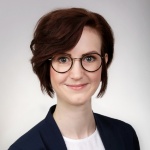
Larissa Born
Dr.-Ing.Deputy Director