The research project "3D braided nodes" focuses on the investigation of external FRP reinforcement for concrete load-bearing structures. The focus of the project is the investigation of structural nodes consisting of a concrete core and a braided FRP hull. The FRP hull can absorb the tensile forces induced by bending moments on the one hand and increase the compressive strength of the concrete core by its confinement on the other hand.
Typically, structural nodes are made of steel, which are manufactured in an energy-intensive and costly process. The FRP structural nodes are an alternative to this, which not only uses less energy in the production of the nodes but also offers greater geometric design freedom. The textile preforms can be adapted cost-effectively to complicated free-form shapes, allowing complex three-dimensional geometries with many variants to be realized.
The preform of the FRP hull is manufactured using a triaxial braid, which is produced in a specially adapted and patented braiding process. Production is a multi-stage process in which two arms of the knot are braided in each braiding step. After impregnation with a matrix system adapted to the application and subsequent curing, a thin-walled, dimensionally stable hull is created. The FRP hull not only serves as reinforcement for the concrete, but also as lost formwork for the concrete filling.
The primary aim of the project is to further advance the existing technology to a level that will enable the industrial production of multi-branched load-bearing structures. This requires an expansion and full automation of the existing braiding process, which currently still requires manual interaction. The braiding method must be modified in a way that these interactions can be completely performed by two six-axis robots.
A detailed examination of the material composition of the FRP hull is necessary, considering not only the mechanical properties but also civil engineering requirements such as weather and fire resistance and stability against alkaline concrete. In addition, the global warming potential of the material composition is analyzed in order to minimize the CO2 footprint of the supporting structures. The material studies form the basis for the development of a simulative material-node-model, which makes the properties of such a node predictable and enables a standardized design.
In order to increase the efficiency and resource conservation of the process, the previously used braiding cores are being replaced by reusable sand cores. It is necessary to adapt the composition and design of the sand cores in order to withstand the process forces that can occur during braiding and impregnation of the preform. Furthermore, the sand core must be specially sealed to prevent the penetration of resin.
Project Duration
September 2023 – August 2026
Project Team
ITFT Institute for Textile and Fiber Technologies, University of Stuttgart
Prof. Dr.-Ing. Götz. T. Gresser, Dr.-Ing. Larissa Born, Robert Wegner
ITKE Institute of Building Structures and Structural Design, University of Stuttgart
Prof. Dr.-Ing. Jan Knippers, Dr.-Ing. Axel Körner, Weiqi Xie
Maus Modell- und Formenbau GmbH, Karlsruhe
Mathias Maus, Frank Heidbrink
Munich Composites GmbH, Putzbrunn
Christian Lichtenberg, Tobias Knaier
Associated Partners
Ed. Züblin AG, Stuttgart
Hans-Jörg Brahms, Martin Benz
Funding
The project „3D braided node“ is funded by the Federal Ministry for Economic Affairs and Climate Action (BMWK) based on a resolution of the German Bundestag as part of the Technology Transfer Program Lightweight Construction (TTP LB; funding code 03LB2084B).
Project Management: Projekträger Jülich (PtJ)
Contact
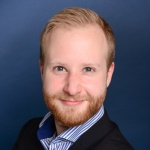
Dipl.-Ing. Robert Wegner
Research Associate